The growing integration of our physical world with virtual environments and smart technology has sparked the Fourth Industrial Revolution (or Industry 4.0). At the forefront of Industry 4.0 is big data, machine learning, artificial intelligence, Web 3.0, and the metaverse. Digital twin technology is another key pillar of Industry 4.0, and it’s disrupting numerous industries, systems, and processes. Read on if you want to learn more about digital twin technology and how it’s transforming the world around us for the better.
What is a Digital Twin and How Do They Work?
A digital twin is a digital representation that serves as the real-time virtual counterpart of a physical object, service, or process. Anything that exists in the physical world—such as cars, human patients and their organs, buildings, and even entire cities—can be reproduced digitally in the form of digital twins.
Digital twins are vital because they allow professionals to virtually test scenarios for their products, processes, facilities, and projects before implementing them in the real world. A digital twin can also be described as a computer program that integrates all of the real-world data associated with the process or system that it’s trying to mirror.
The data used to run digital twins is generally collected from internet of things (IoT) devices, sensors, HMIs, edge hardware, and other embedded devices. This data is used to construct simulations that can accurately predict how a product, project, or process will perform.
A Digital Twin can be used in a wide variety of industries—including healthcare, manufacturing, disaster management, surveying and mapping, as well as environmental resource management.
During the early stages of development, experts in data science or applied mathematics will research the physics and operational data of a physical system or object. This is done in order to develop a mathematical model that simulates the prototype.
It’s vital that the digital twin is able to receive feedback from sensors that gather data from the real-world prototype. This allows the digital twin to accurately mirror and simulate the prototype in real-time.
Digital twin technology can be broadly classified into three types: the digital twin prototype (DTP), the digital twin instance (DTI), and the digital twin aggregate (DTA).
- Digital twin prototype (DTP) – This serves as the prototype of a physical asset, making it a vital part of product development. Ideally, the DTP should stay linked to its physical counterpart throughout its lifecycle.
- Digital twin instance (DTI) – This is simulated once a product has been manufactured in order to run tests on various usage scenarios. A DTI starts with baseline data from the DTP but gradually becomes enriched with operational data throughout its lifecycle.
- Digital twin aggregate (DTA) – This stage gathers DTI data in order to run prognostics, test operating parameters, and determine the overall functionality of a product. Note that a DTA is an aggregate of many DTIs and is simulated to understand group behavior rather than individual behavior (e.g. all the wind turbines in a wind farm rather than just one wind turbine).
What Is the Difference Between a Digital Twin and a Simulation?
While digital twins and simulations both use digital model-based simulations, digital twins go beyond simply imitating the operations and processes of a system. While traditional simulations run virtual environments that mirror a physical counterpart, they do not integrate real-time data. In contrast, digital twins receive real-time data from their physical counterparts, enabling them to mirror the prototypes’ current performance.
When using a digital twin, the physical object is outfitted with sensors that generate data about various aspects of the object’s performance. The resulting data is then relayed to a processing system and applied to its virtual counterpart. This real-time flow of data is two-way (i.e. data from the digital twin can also be transmitted back to the physical object via the sensors).
In other words, while simulations can replicate what is happening to products, processes, or systems, they’ll remain static unless they’re fed additional data. Digital twins, in contrast, will replicate what is happening to real-world products, processes, and systems thanks to the two-way flow of data.
Another key difference is the scope of use: while CAD-based simulations enable professionals to test various scenarios against set parameters, digital twins have a much broader scope. Digital twins can encompass all stages of a product’s lifecycle, not just design development.
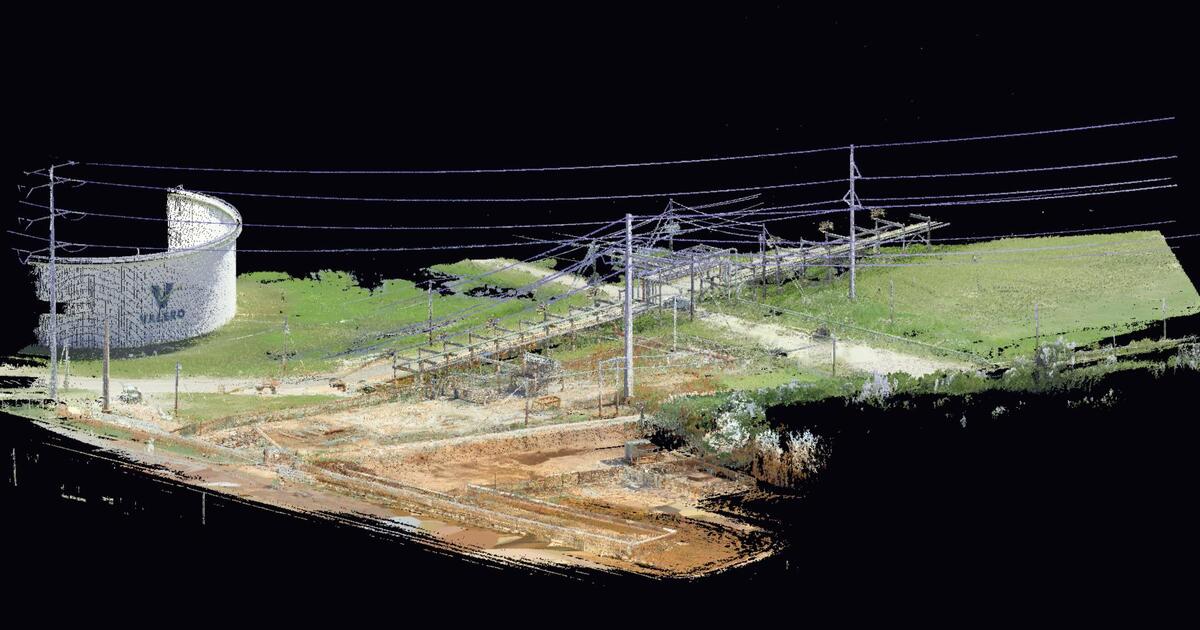
What are the Different Types of Digital Twins?
A digital twin can follow a bottom-up structure, with the lowest level delivering the simplest and most limited data. Each succeeding level delivers more sophisticated and diverse types of data.
Component Twins/Parts Twins
These types of digital twins are the virtual counterparts of single components that make up a system or product. Only the key components that have a direct impact on performance and functionality are digitally twinned.
Asset Twins
These are the next level of digital twins and focus on describing how individual components work together as a cohesive asset. Asset twins may receive data from component or parts twins, or be a collection of component twins themselves.
Asset twins allow you to evaluate an entire system, enabling you to assess how individual components work together, as well as identify areas for improvement.
System or Unit Twins
These types of digital twins function on a higher level. They fuse individual asset twins, giving you the opportunity to assess how individual assets work together.
Process Twins
Process twins examine products, systems, and processes from a macro level. They provide high-level insights into the collaboration of all units.
When Was Digital Twin Technology Invented?
The concept of a digital twin was first proposed by the American writer and computer scientist David Gelernter in his book Mirror Worlds. In his revolutionary book, Gelernter envisions a future society where the real world is reproduced virtually. Published in 1991, Mirror Worlds anticipates current technological disruptions, like the metaverse and virtual reality.
Michael Grieves, former chief scientist at the Florida Institute of Technology, first applied the digital twin concept in manufacturing. The concept was first introduced by Grieves at the Society of Manufacturing Engineers Conference held in Troy, Michigan, in 2002.
While the concept was known by various names, the term “digital twin” was coined by NASA principal technologist John Vickers in a 2010 Roadmap Report.
What are the Benefits of Digital Twin Technology?
Digital twins offer numerous benefits, depending on their application and objectives. They allow different businesses to identify areas for improvement, as well as optimize safety, processes, and performance.
In product development and manufacturing, digital twins allow companies to test and validate their products, refining them before they even exist in the real world. By digitally creating a replica of the planned production process, digital twins allow engineers to identify any process gaps or failures before production and launch.
A digital twin also plays a key role in predictive maintenance. Since the sensors generate big data in real-time, problems can be identified quickly. This allows businesses to more accurately schedule repairs and replacements before components break down.
Other benefits include process improvements (e.g. aligning staffing levels with production demand) and improving workplace safety (e.g. reducing the risk of hazardous material spills).
A digital twin can also be combined with other technologies to achieve mutual goals. Fenstermaker utilized LiDAR mapping to complete a major laser scanning project. The purpose of the project was to capture sufficient data to create piping and instrumentation diagrams, isometric drawings, and a digital twin model for a unit with no as-built records.
What are the Industries and Markets that Use Digital Twins?
Engineering
There are now people using a digital twin in nearly every facet of engineering. Digital twin engineers create virtual representations of physical assets, systems, and structures. This allows them to gauge how IoT-connected entities interact with and respond to their environment.
Automobile Manufacturing
You can also use a digital twin in the automotive industry to create virtual counterparts of physical vehicles. Different sensors are used to capture the behavioral and operational data of the vehicle. The resulting data is then used to analyze the overall vehicle performance and improve customer service.
Aircraft Production
In the aviation industry, you can use a digital twin to assist in the development of new aviation products, as well as make improvements to existing products more quickly. Boeing used digital twin technology to assess how materials would perform throughout their aircrafts’ lifecycle. This allowed them to improve the quality of some components by 40%.
Railcar Maintenance
Alstom, a rolling stock manufacturer with a stake in the global rail transport market, used digital twin modeling to optimize predictive maintenance for the Pendolino train fleet on the West Coast Main Line (WCML) in the United Kingdom.
Digital twin modeling was used to reduce unnecessary railway maintenance expenses and to simulate potential events and emergencies to optimize disaster preparedness.
Building Construction
A digital twin can also be used to create exact replicas of construction projects and assets. This could be a single building, a building complex, or even an entire city. These digital models help improve the analytical capabilities of building information modeling (BIM).
Manufacturing
A digital twin has a wide array of use cases in manufacturing, including improving system designs, testing and refining new products, monitoring and preventive maintenance, and asset lifecycle management.
Power Utilities
They are also widely used to improve and test utility system designs, assist with predictive maintenance, and help grid operators monitor overall efficiencies.
What Does the Future Hold for Digital Twin Technology?
The global digital twin market is forecasted to grow exponentially over the coming years. According to MarketsandMarkets, the global digital twin market was valued at $3.1 billion in 2020. This valuation is expected to reach $48.2 billion by 2026—a CAGR of 58% over the forecast period.
Numerous factors are responsible for the accelerated adoption of digital twin technology among organizations. Chief among them is the growing sophistication of artificial intelligence (AI), the industrial internet of things (IIoT), and data science. Other factors include the rapid development of digital manufacturing and digital health solutions, and the growing demand for real-time monitoring data and predictive maintenance.